|
 |
 |
extrusion aluminum |
Indirect Extrusion
In indirect extrusion, also known as backwards extrusion, the billet and container move together while the die is stationary. The die is held in place by a "stem" which has to be longer than the container length. The maximum length of the extrusion is ultimately dictated by the column strength of the stem. Because the billet moves with the container the frictional forces are eliminated. This leads to the following advantages:
A 25 to 30% reduction of friction, which allows for extruding larger billets, increasing speed, and an increased ability to extrude smaller cross-sections
There is less of a tendency for extrusions to crack because there is no heat formed from friction
The container liner will last longer due to less wear
The billet is used more uniformly so extrusion defects and coarse grained peripherals zones are less likely.
The disadvantages are:
Impurities and defects on the surface of the billet affect the surface of the extrusion. These defects ruin the piece if it needs to be anodized or the aesthetics are important. In order to get around this the billets may be wire brushed, machined or chemically cleaned before being used.
This process isn't as versatile as direct extrusions because the cross-sectional area is limited by the maximum size of the stem. |
|
|
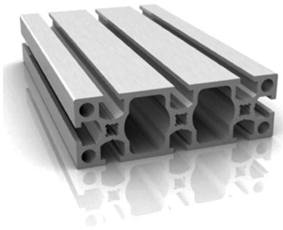 |
|
|
 |